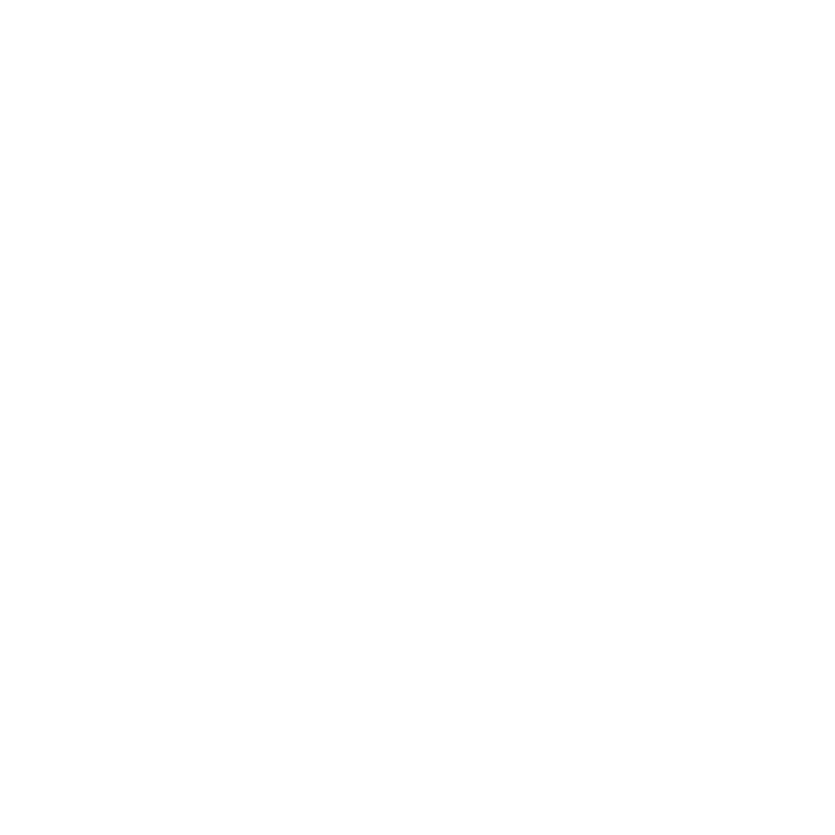
Demand Planning and Production Optimization
About Nestlé
16
PLANTS
100
PRODUCTION LINES
1350
SKUS
6
SALES CHANNELS
For over 100 years, Nestlé has been dedicated to food production. It has more than a dozen product families, including global icon brands and local favorites, with more than 1350 different SKUs. Among the product families that Nestlé Brazil produces and sells there are: beverages, coffees, dairy products, cereals, chocolates, nutrition, baby food and even pet food.
The project challenge
Until now, no tool had the flexibility and speed that Nestlé required to plan the Demand and Production processes in an integral way and within the same environment.
Production planning is essential for optimizing the overall process, considering the products, resources and processes involved, as well as the expected demand for each product line.
Nestlé sought to find a tool that automates and optimizes the Demand and Production Planning processes, in a way that would allow users to have full visibility of both the hierarchy of its large product portfolio (by segment, family, brand, SKU, among others) and the logistics point, factories and production lines.
Solution Design
The proposed solution system integrated the existing Distribution Module, with the Demand Planning and Production Optimization Modules.
Demand Planning Module
The aim was to develop a single planning model, based on existing models and best practices. This module included forecast adjustments to the Baseline, BIAS analysis, trend and evolution analysis, trade marketing alignment, risk analysis and volume division by SKU.
Production Optimization Module
With the implementation of this module, the major challenge was to develop the Master Production Schedule, which established the Mixing, Volume and Production Deadlines considering sales, operations and stock planning.
Benefits achieved by Nestlé
Optimizing production by identifying possible bottlenecks in the process in advance.
Matching production to demand, optimizing stock levels, avoiding shortages or lost sales.
Anticipating resource needs: inputs, labor or investments in production line capacity.
Automation of different processes saving up to 75% of the invested time in carrying out operational tasks.